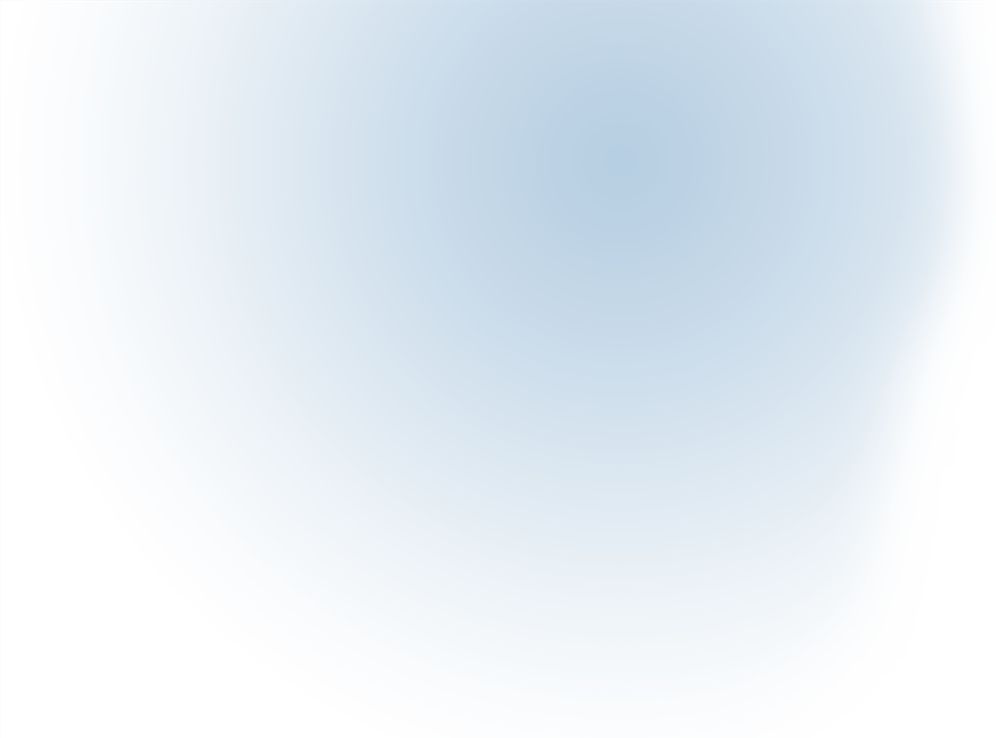
Diversified Heat Transfer (DHT) is a leading solution provider of heat exchange equipment and systems. Due to continued growth and success, our team is always seeking quality people. Please review the below list of job opportunities and forward all resumes to careers@dhtnet.com. At DHT we are committed to a culturally diverse workforce. DHT is an equal opportunity employer.
Current DHT Opportunities:
- Junior Sales Engineer
- Welder Combination
- Traffic Clerk
- Assembler
Junior Sales Engineer
DHT is offering an exciting opportunity for a Jr. Sales Engineer to join their fast-growing team in the HVAC industry. The Jr. Sales Engineer will play a key role in supporting heat transfer product sales, both on job sites and through in-office client relationships. To achieve this, the Jr. Sales Engineer will work closely with manufacturer representatives, contractors and facilities personnel throughout the NY/NJ area to ensure that sales goals are met, and customers are satisfied. The Jr. Sales Engineer is also responsible for the overall product selection and design meet application needs including functionality, material, and test requirements while staying within cost targets.
DHT is committed to providing the necessary support and training to ensure the success of this role. As a result, the Jr. Sales Engineer will be trained to become a technical advisor and advocate for the products, providing expert advice to clients on product selection and use.
If you are a self-starter who thrives in a fast-paced environment and is passionate about the HVAC industry, we encourage you to apply for this exciting opportunity.
This is a hybrid position where 75% will be on job sites or conducting customer visits in the NY/NJ metropolitan area. The remaining 25% of the time will be spent working from home and/ or at the DHT main office in Towaco, NJ.
Responsibilities Include:
- Conduct site visits to measure and gather data, evaluate product selection, and provide quotes.
- Call on major accounts, negotiate sales prices and discounts in consultation with management.
- Utilize Genius ERP to provide quotes and follow up on sales orders to ensure on-time delivery.
- Provide Sales and Rep Support by assisting with quoting, spec review, and submittals in the sales engineering process.
- Provide technical support for pre and post-sales.
- Provide Customer Support to engineers, contractors, and end-users.
- Participate in weekly team meetings.
- Create and maintain project timelines and provide weekly/ monthly status updates to management.
Qualifications:
- 0-2+ years’ experience in HVAC industry and or mechanical engineering.
- Bachelor’s in mechanical engineering a plus.
- Knowledge of mechanical, electromechanical, hydraulic controls, machining operations, welding, and brazing is preferred.
- Advanced analytical skills
- Highly motivated self-starter, capable of working independently and able to drive concepts to completion.
- Excellent organization, presentation, oral and written communication skills to convey complex information in a clear, concise manner
- Ability to collaborate across multi-disciplinary functions (engineering, sales, operations)
- Excellent written and verbal skills. Solid public speaking skills; able to present ideas, conclusions, and recommendations with clarity to diverse business audiences.
- Strong attention to detail, and excellent organization and time management skills.
- Proficient in all Microsoft Office applications (Word, Excel, PowerPoint).
Interested Candidates should send resumes to Careers@dhtnet.com with the Subject “Jr. Sales Engineer”.
Welder Combination
The Welder Combination will follow standard welding procedures and techniques to optimize Flux Cored Arc, Stick, MIG, TIG, and plasma welding processes on steel, stainless steel, aluminum, and nickel materials. These processes will be used to weld pressure vessels and structural steels. Pressure vessel welding must meet all applicable ASME and TEMA specifications and pass X-Ray, die penetrant and visual inspections.
Responsibilities include the following:
- Pass ASME coupon tests and obtain ASME Certified Combination Welder
- Weld mig, tig, and stick pressure vessels and structural steels
- Use quality assurance instruments
- Ensures equipment is maintained and quality standards are met with all products
- Read blue prints according to weld specifications and blueprints
- Review engineering change orders (ECO’s) and implement desired changes
- Follow all safety policies and PPE requirements
- Follow standardized processes.
- Must adhere to “5S” standards daily
Requirements:
- Technical Degree/2 year minimum mig, tig, stick welding experience in manufacturing environment or combo of education and work experience
- Must be mechanically inclined.
- English comprehension: Ability to read, write and communicate
- Ability to handle light and average weight parts.
- Ability to use hand and power tools.
- Ability to listen and learn from instructions, cooperate and participate in the department’s training program
- Ability to work safely
- Must be flexible with assignment changes needed to fulfill production needs
- Ability to work both independently and as part of a group
Interested Candidates should send resumes to Careers@dhtnet.com with the Subject “Welder Combination”.
Traffic Clerk
In coordination with the Production Supervisor and Plant Operations Manager, the Traffic Clerk is responsible for Shipping, Receiving, Storing, and Issuing of equipment, tools, and supplies, maintaining inventory control, packaging, crating and performing the required record keeping.
ESSENTIAL DUTIES AND RESPONSIBILITIES include the following: The Traffic Clerk is responsible for Shipping, Receiving, Storing, and Issuing of equipment, maintaining inventory control, packaging, crating and inbound/outbound customer calls as required.
Receiving:
- Expedite discrepancies upon request
- Deliver received materials
- Unloading trucks
- Detailed checking of material
- Matching of material to packing slips
- Matching of packing slips to purchase orders
- Tagging and identification of material & investigating discrepancies
- Notifying end users of arrival of material
- Filing documents
- Posting of inventory receipts to computer
- Copying documents and distribution of documents to accounting
Shipping:
- Preparing bills of lading and freight way bills
- Loading/unloading trucks
Interested Candidates should send resumes to Careers@dhtnet.com with the Subject “Traffic Clerk”.
Assembler
Assemble and test a variety of tube bundles, coils, and shells. The assembler will complete final assembly, test , and quality control of all parts.
Responsibilities include the following:
- Handle light, heavy and average weight parts.
- Use hand and power tools.
- Accurately complete all sub-assemblies prior to installation on unit.
- Mount and connect auxiliary, mechanical, electrical, electronic, pneumatic or hydraulic
equipment. - Assemble a variety of products from blueprints and drawings.
- Ability to fit parts to close tolerances.
- Must be mechanically inclined.
- Listen and learn from instructions.
- Cooperate and participate in the department’s training program.
- Participate in all 5S initiatives.
- Other duties as assigned.
Requirements:
- At least 2 years of experience in assembly in a manufacturing environment.
- English Comprehension
- Good verbal and written communication skills
- Good mechanical aptitude
- Ability to lift up to 50 lbs
- Ability to adapt to changing responsibilities
Interested Candidates should send resumes to Careers@dhtnet.com with the Subject “Assembler”.